

Work Areas

The aim of the project is to prepare bio-based polymers that can replace conventional fossil-based polymers. The bio-based polymers will have both the required functionality and be more sustainable than traditional petroleum based products. They will be provided for a range of applications, such as homecare products and coatings.
The project has two main work areas that are summarised below:
​
Work Area 1: Making bio-based polymers
​
Polymers are made from joining together building blocks called monomers. In this project, two types of monomer, a Michael donor and a Michael acceptor, will be joined together via an aza-Michael reaction.
​
​
​
​
​
​
General information about monomers and polymers can be found on the Britannica website.
Step 1: Making the monomers and polymers (lab-scale)
​
Scientists at the University of York, Wageningen Food and Biobased Research, Circa and AVA Biochem will prepare monomers and polymers from bio-based starting materials. Key to this work will be the development of green, sustainable and scalable process for the synthesis of the Michael donor and acceptor molecules. These monomers will be derived from bio-based platform molecules, many of which have been developed by members of the consortium, namely levoglucosenone (Circa) and 5-hydroxymethylfurfural (Ava Biochem). The most promising polymers will be carried on to the second stage of development.
​
Step 2: Produce sufficient amounts for testing (pilot-scale)
​
The second phase of the research program will see the specialists at VTT take the protocols from the lab based chemistry and adapt them to make large enough quantities for testing.




Work Area 2: Testing and assessing the polymers
To be successful replacements, the project will demonstrate that the polymers:
-
work in the target applications
-
are safer
-
can be made at an industrial scale
-
have a reduced environmental impact
Step 3: Safety testing
​
To address the safety concerns with the existing fossil-based polymers, BioDetection Systems will monitor the toxicity of the polymers using a panel of CALUX® assays. VOC emission testing will also be performed, as this is relevant for some of the applications.
​
Step 4: Assessments
Four types of assessments will be conducted to analyse the road from lab to industrial application:
In order to transfer the technology from the lab to industrial scale the conceptual process design is developed for different candidates (monomers, polymers and materials). Outputs of the process design are used as inputs for the following assessment types.
1. Process design



2 Techno-economic evaluation
The designed process is further evaluated on technical and economical viability. The final output of this step is the production cost, which is estimated as a sum of contributions relating to capital expenditure (CAPEX) and to operating expenditure (OPEX).



3 Environmental impact (LCA) and sustainability assessments
To evaluate the potential impacts associated with CHAMPION products and guide the process optimisation towards sustainable solutions.



4 End-of-life options and circularity
Including biodegradability assessments and recycling options.



​
The Process Design Center (PDC) will conduct assessments 1 and 2 with nova-Institut (environmental evaluations) and SQ Consult (sustainability performance) completing assessment type 3. OWS leads on assessment 4, with end-of-life options including recycling and biodegradability.
Step 5: Testing in target applications
​
Based on industry-partner interest, four target applications are selected to test the performance of the bio-based polymers:
Coatings - Orineo
Orineo aims to extend its portfolio of bio-based table and kitchen surface coatings with products with improved end-of-life options and a wider range of bio-based feedstocks than currently achieved.

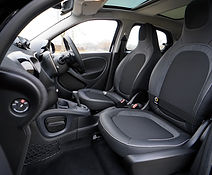
Car interior surfaces – Stahl
Continuing its aim towards a reduced environmental footprint, Stahl’s interest in the project includes the use of more bio-based products to reduce carbon emissions. They are targeting improved end-of-life options and a reduction on the reliance of polyurethane.
Structural adhesives – Scott Bader Company
These adhesives demand high performance in both strength and stability, meaning end-of-life options are limited. Scott Bader are targeting sustainable replacements for the fossil-derived starting materials and improved end-of-life options.


Home care formulations - Unilever
Home care formulations have limited end-of-life options. There is no real opportunity for recycling, as the used product is emptied directly into the drains from e.g. washing machines and dishwashers. Unilever are interested in polymers that meet the challenge of high performance and biodegradability and which help eliminate our use of virgin fossil fuels.